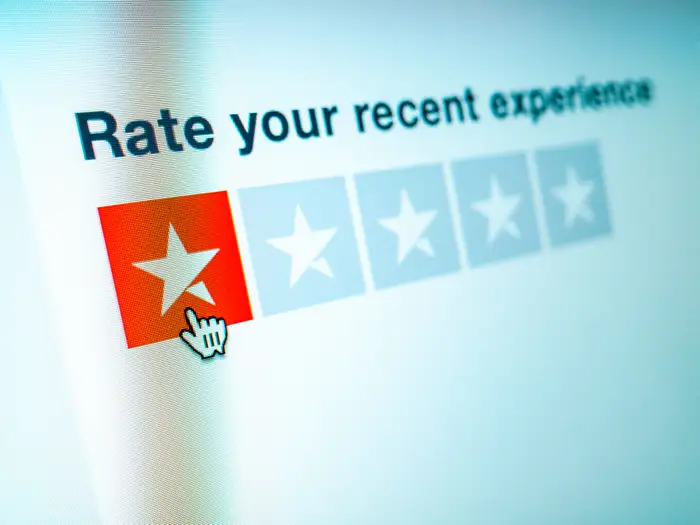
How a 10% Underweight Anode Nearly Drowned My Client’s Reputation
Mark slammed his phone down after reading the latest one-star review: “You short-weigh these by 15% – do you even own a scale?”
Within weeks, his marine-supply business saw Q2 sales plummet by over 10%. He’d already burned through €12,000 on a “brand repair” marketing campaign, but it was useless. The negative reviews, all detailing underweight and faulty anodes from his supplier, kept pouring in. His reputation was being systematically dismantled by a product he’d trusted.
This wasn’t a quality issue. This was fraud.
Three Ways “Bargain” Anodes Become Your Liability
Mark’s nightmare was caused by three specific, all-too-common failures in the low-cost anode supply chain:
1. Weight Theft (The 10% Material Loss): The simplest way to cheat. A supplier sells you a 10kg anode but ships 9kg of material. That “missing” metal is pure profit for them and a guarantee of premature corrosion for your client.
2. Botched Casts & Fit Failures: To save money, old, warped molds are used, and finishing is skipped. The result? Off-center bolt holes, warped straps, and rough surfaces that make installation a nightmare for the end-user, stalling projects and generating furious complaints.
3. Impurity Passivation: The most insidious failure. Low-grade, recycled zinc is contaminated with iron or lead. Within weeks, the anode forms a hard, useless crust. It stops working entirely, leaving the vessel’s expensive hull and machinery to corrode instead.
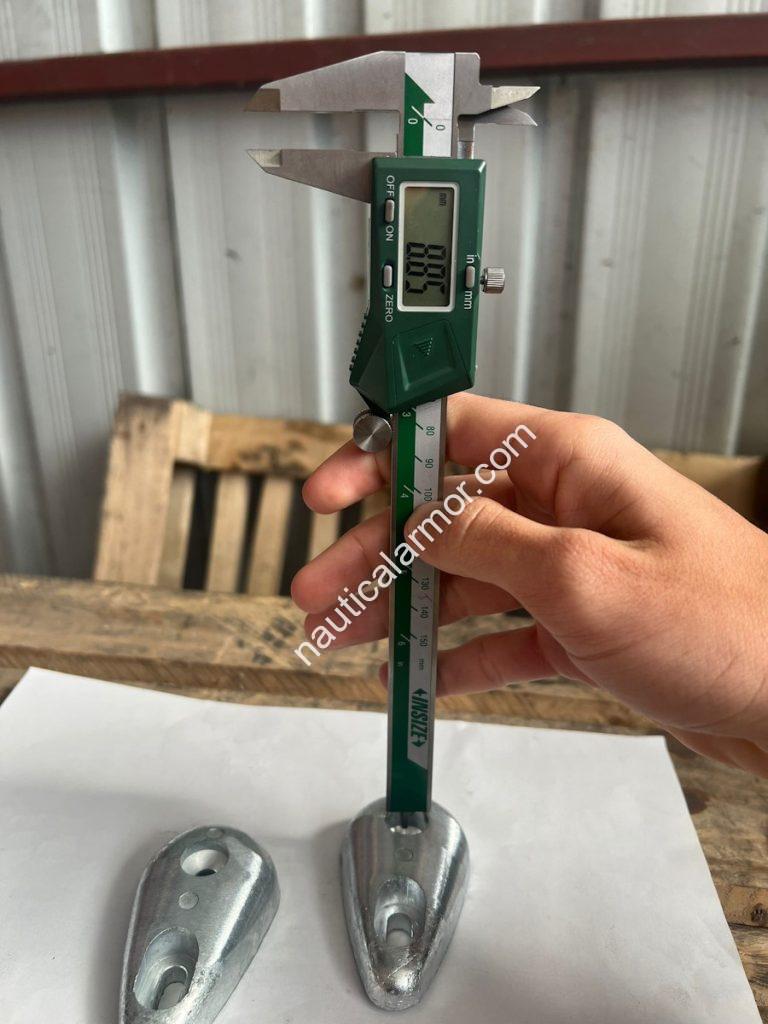
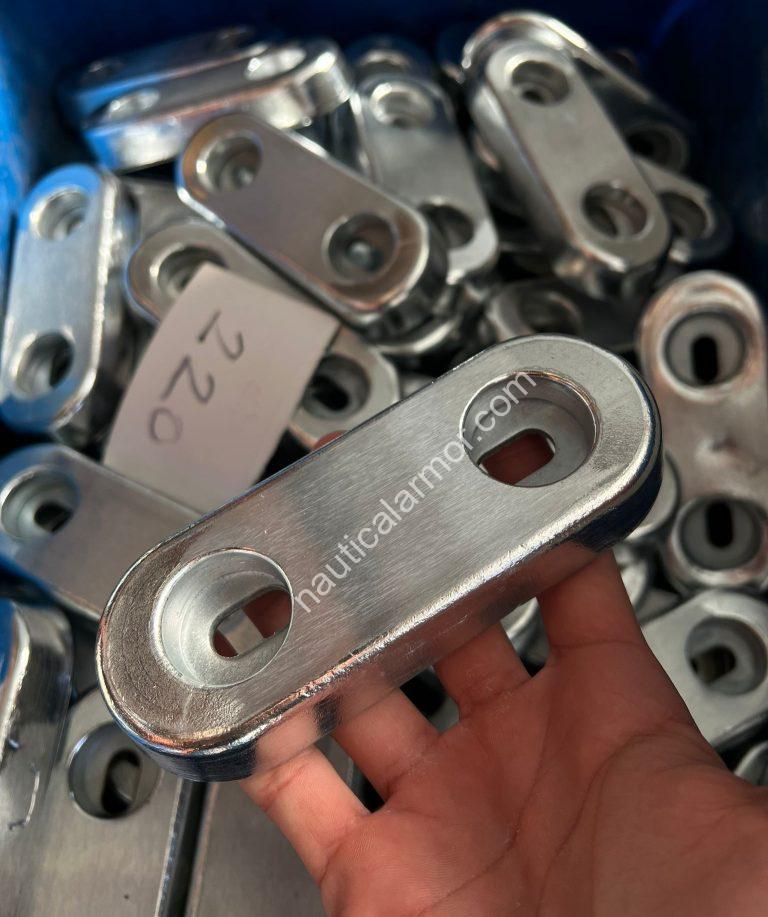
Mark needed more than promises. He needed iron-clad proof. So we built him a process that locks out every cheap-anode scam.
The Nautical Armor Solution: A Verifiable, Iron-Clad Process
We didn’t just sell Mark new anodes. We gave him a documented system of quality he could stand behind.
• Guaranteed ±3% Weight Tolerance: We don’t just promise accuracy; we guarantee it. Every batch is sample-weighed to ensure what you order is what you get. No short cuts.
• Precision Molds & Perfect Fit: Our molds are meticulously maintained and refreshed to prevent casting flaws. This ensures every anode has clean, perfectly aligned bolt holes and securely bonded straps for seamless installation.
• The 33% Pre-Shipment Audit with Photo Log: I personally inspect one-third of every order before it ships. I then send our partners a PDF with photos from their specific batch’s QC check, providing tangible proof of quality they can show their own teams and clients.
The Result
Four months after switching to Nautical Armor, the one-star reviews on Mark’s online stores vanished. His average rating climbed from a disastrous 3.2 to a stellar 4.8 stars. By Q4, his sales had not only recovered but had jumped significantly, beating their previous year’s peak.
He stopped selling a product and started selling verifiable reliability.
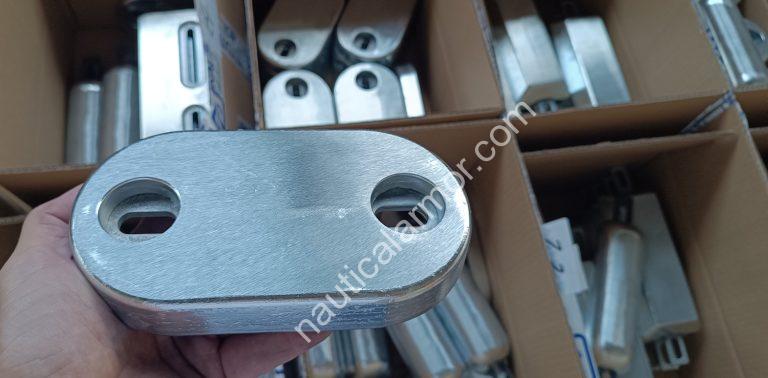
Ready to Partner with a Producer You Can Trust?
Choose the first step that’s right for you:
A) See Your True Cost of Cheap Anodes: Email your parts list to gvapo@nauticalarmor.com for a side-by-side report comparing price vs. total liability.
B) Book a ‘Liability Lockdown’ Call: Worried about your current supplier? Let’s schedule a 15-minute call to map your hidden risks.
C) Get Our ‘Instant Planning Kit’: Email me with the subject “Planning Kit” for our catalog and a transparent overview of our QC process in a downloadable PDF.
GVAPO
Nautical Armor